Sikafloor®-2350 ESD
Sikafloor®-2350 ESD is een 2-componenten, zelfvloeiende, gekleurde, elektrostatisch dissipatieve vloercoating op basis van epoxyhars.
- Betrouwbare lange termijn geleidbaarheid
- Voldoet aan de ESD eisen
- Lage VOS emissie
- Goede weerstand tegen afschuring
- Weinig geurafgifte tijdens de verwerking
- Zeer goede mechanische weerstand
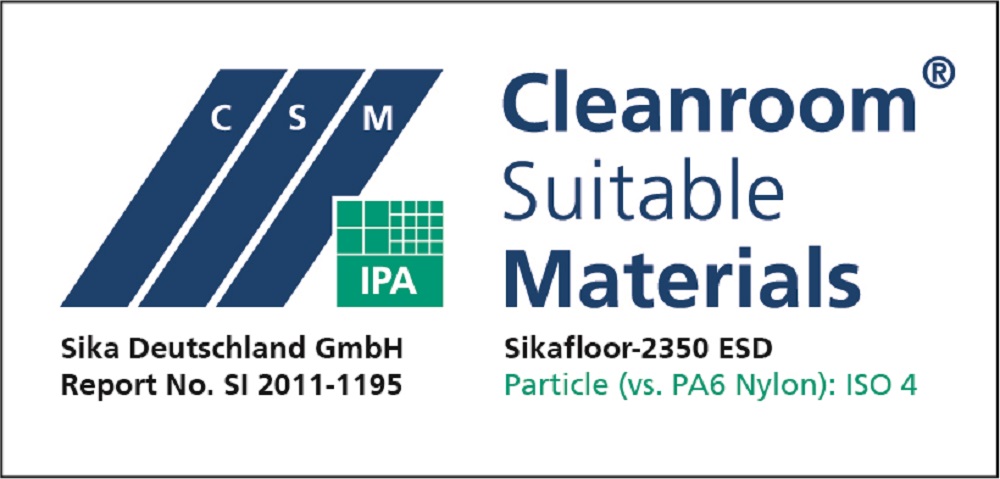
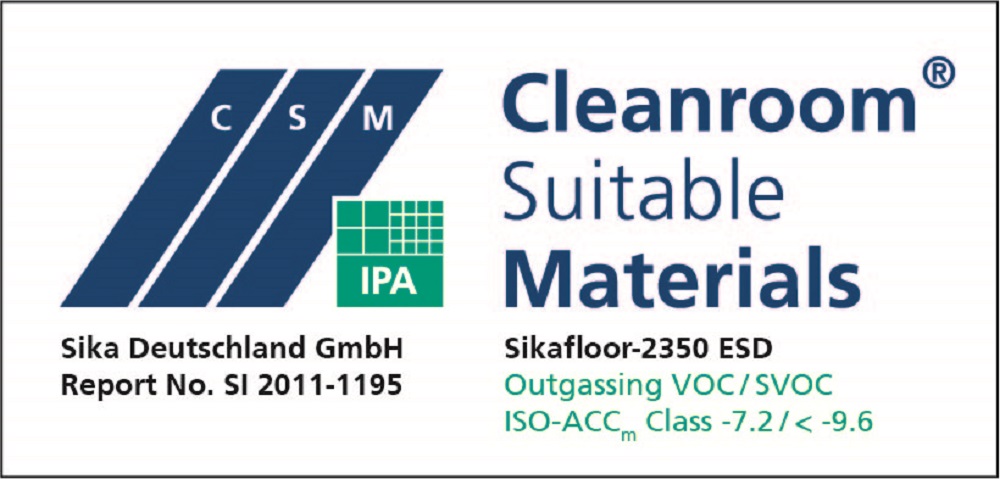
Gebruik
Het product kan worden gebruikt als:- Gladde, elektrostatisch geleidende vloerbedekking
- Het product mag alleen worden gebruikt voor binnentoepassingen.
Voordelen
- Betrouwbare lange termijn geleidbaarheid
- Voldoet aan de ESD eisen
- Lage VOS emissie
- Goede weerstand tegen afschuring
- Weinig geurafgifte tijdens de verwerking
- Zeer goede mechanische weerstand
Verpakking
Component A | 24,6 kg |
Component B | 5,4 kg |
Component A + Component B | Set van 30 kg |
Kleur
Component A | Gekleurd, vloeibaar |
Component B | Transparant, vloeibaar |
Kleur uitgehard product | Beschikbaar in de volgende RAL kleuren (bij benadering): RAL 6027, RAL 6033, RAL 6034, RAL 7005, RAL 7015, RAL 7016, RAL 7030, RAL 7032, RAL 7035, RAL 7040, RAL 7047 |
Blootstelling aan direct zonlicht
Nota: Onder invloed van direct zonlicht kan enige verkleuring en kleurafwijking optreden. Dit heeft echter geen invloed op de functionaliteit en prestaties van de coating.
Productdetails
MILIEU-INFORMATIE
- Conform met Materialen en middelen (MR): productverelding en optimalisering van bouwproducten - Materiaal ingrediënten onder LEED® v4
- Conform met Materialen en middelen (MR): productvermelding en optimalisering van bouwproducten — Milieuproductverklaringen onder LEED® v4
- Conform met de Indoor Environmental Quality (EQ): Materialen met een lage uitstoot onder LEED® v4
- Milieuproductverklaring (EPD) in overeenstemming met EN 15804. EPD onafhankelijk geverifieerd door Institut für Bauen und Umwelt e.V. (IBU)
- Voldoet aan de eisen van AgBB inclusief de LCI-waarden (augustus 2018) voor gebruik in binnenmilieu.
- Franse regelgeving inzake VOS-emissies binnenshuis klasse A+
GOEDKEURINGEN / NORMEN
- CE markering en prestatieverklaring volgens EN 13813:2002 — Dekvloermortel en dekvloeren - Dekvloermortels - Eigenschappen en eisen - kunstharsgebonden dekvloermateriaal
- CE markering en prestatieverklaring volgens EN 1504-2:2004 — Producten en systemen voor de reparatie en bescherming van betonconstructies - Oppervlaktebeschermingssystemen voor beton - coating
- Slipweerstand volgens DIN 51130, Roxeler, Certificate Nr. 020243-20-3
- Slipweerstand volgens DIN 51130, Roxeler, Certificate Nr. 020243-20-2
- Slipweerstand volgens DIN 51130, Roxeler, Certificate Nr. 020243-20-2a
- Goedkeuring voor ESD-beschermende producten volgens IEC 61340-5-1, RISE-instituut, nr. ESD-20-0023
- Deeltjesemissie volgens ISO 14644-1, Sikafloor®-2350 ESD, CSM Fraunhofer, SI 2011-1195
- Isolatieweerstand volgens DIN VDE 0100-600, Kiwa, Testrapport nr. P 12819-E
- Outgassing gedrag volgens ISO 14644-15, CSM uitspraak over kwalificatie, Fraunhofer IPA
- Outgassing gedrag, VOC/ SVOC, CSM Fraunhofer, certificaat nr. SI 2011-1195
Chemische basis
Epoxy
Houdbaarheid
18 maanden vanaf de productiedatum
Opslagcondities
Het product moet opgeslagen in de originele, ongeopende en onbeschadigde verpakking, in droge omstandigheden, en bij temperaturen tussen +5°C en +30°C. Altijd de verpakking raadplegen.
Raadpleeg het meest recente veiligheidsinformatieblad voor informatie over een veilige verwerking en stockage van het product.
Dichtheid
Component A | ~1,70 kg/l |
Component B | ~1,00 kg/l |
Gemengd product | ~1,5 kg/l |
Vaste stofgehalte in gewicht
~100 %
Vaste stofgehalte in volume
~100 %
Shore D hardheid
~80 (na 7 dagen bij +23 °C) | (EN ISO 868) |
Slijtvastheid
~1,29 g, hars voor 20% gevuld met kwartszand (H22/1000/1000) (na 7 dagen bij +23°C) | (EN ISO 5470-1) |
Druksterkte
~120 N/mm² | (EN ISO 604) |
(uitgehard na 28 dagen bij +23°C) |
Buigtreksterkte
~30 N/mm² | (ISO 178) |
(uitgehard na 28 dagen bij +23°C) |
Hechtsterkte bij trek
> 1,5 N/mm² (betonbreuk) | (EN 1542) |
Elektrostatisch gedrag
Aardweerstand | Rg < 109 Ω |
Typische gemiddelde aardweerstand | Rg ≤ 105 Ω tot 107 Ω |
Opbouw lichaamsspanning | < 100 V |
Systeemweerstand (persoon/vloersysteem/schoeisel) | < 109 Ω |
Opmerking: Meetresultaten kunnen worden beïnvloed door ESD kleding, omgevingsomstandigheden, meetapparatuur, de testpersonen en reinheid van de vloer.
Thermische resistentie
Korte termijn, maximaal 7 dagen | +60 °C |
BELANGRIJK:
Gelijktijdige mechanische en chemische belasting
Terwijl het product wordt blootgesteld aan temperaturen tot +60 °C, kan gelijktijdige mechanische of chemische belasting schade aan het product veroorzaken.
1. Stel het product niet bloot aan chemische of mechanische belasting bij verhoogde temperaturen
Toepassing
Mengverhouding
Component A : component B | 82 : 18 (in gewichtsdelen) |
Producttemperatuur
Minimaal | +15 °C |
Maximaal | +30 °C |
Omgevingstemperatuur
Minimaal | +15 °C |
Maximaal | +30 °C |
Relatieve luchtvochtigheid
Maximaal 80 % RV
Dauwpunt
Pas op voor condensatie! De temperatuur van de ondergrond en van het niet uitgehard materiaal dient minimaal 3°C hoger te zijn dan het dauwpunt om het risico op condensvorming en witte uitbloeiingen op de vloerafwerking te verminderen. Lage temperaturen en vochtige omstandigheden verhogen het risico op vorming van witte uitbloeiingen
Ondergrondtemperatuur
Minimaal | +15 °C |
Maximaal | +30 °C |
Verwerkingstijd
Temperatuur | Tijd |
+15 °C | 40 minuten |
+20 °C | 25 minuten |
+30 °C | 15 minuten |
Opmerking: Deze tijden zijn bij benadering en worden beïnvloed door veranderende omgevingsomstandigheden, en in het bijzonder door temperatuur en relatieve luchtvochtigheid.
Verwerkt product klaar voor gebruik
Temperatuur | Voetverkeer | Licht belastbaar | Volledig uitgehard |
+15 °C | ~48 uur | ~3 dagen | ~7 dagen |
+20 °C | ~24 uur | ~48 uur | ~4 dagen |
+30 °C | ~16 uur | ~36 uur | ~3 dagen |
Opmerking: Deze tijden zijn bij benadering en worden beïnvloed door veranderende omgevingsomstandigheden, en in het bijzonder door temperatuur en relatieve luchtvochtigheid.
Verbruik
Coatingsysteem | Product | Verbruik |
Gietlaag | Sikafloor®-2350 ESD | 1,5 tot 2,5 kg/m² gevuld met 20 % kwartszand 0,1–0,3 mm |
Gietlaag antislip ingestrooid | Sikafloor®-2350 ESD + Kwartszand 0,7-1,2 mm | 1,1 kg/m² gevuld met 20 % kwartszand 0,1-0,3 mm + 4-6 kg/m² |
Toplaag op instrooilaag | Sikafloor®-2350 ESD | 0,8 kg/m² |
Getextureerde rollaag | Sikafloor®-2350 ESD | 0,7 kg/m² tot 0,8 kg/m² |
Opmerking: Alle waarden zijn theoretisch en zijn afhankelijk van de zuigkracht, ruwheid en vlakheid van de ondergrond, hoogteverschillen, materiaalverlies en andere afwijkingen.
Breng het product aan op een proefvlak om het exacte verbruik te berekenen voor de specifieke omstandigheden van de ondergrond en met het beoogde materieel voor de toepassing.
VERWERKINGSINSTRUCTIES
ONDERGRONDKWALITEIT
Cementgebonden ondergronden (beton/dekvloer) moeten structureel gezond zijn, en een voldoende druksterkte (min. 25 N/mm²) en treksterkte (min. 1,5 N/mm²) bezitten.
Ondergronden moeten schoon en droog zijn, en vrij van alle contaminaties zoals vuil, olie, vet, coatings, cementmelk, oppervlaktebehandelingen, en los, onsamenhangend materiaal.
ONDERGRONDVOORBEHANDELING
BEHANDELING VAN VOEGEN EN SCHEUREN
BELANGRIJK
De onjuiste beoordeling en behandeling van scheuren kan leiden tot een kortere levensduur van het systeem en van uit de ondergrond doorkomende scheuren.
Aansluit-/constructievoegen en bestaande statische oppervlakkige scheuren in de ondergrond dienen voorbehandeld te worden alvorens het systeem aan te brengen. Gebruik Sikadur® of Sikafloor® harsen.
MENGEN
GETEXTUREERDE ROLCOATING
1. Meng eerst component A (hars) met een elektrisch mengtoestel met een enkele mengstaaf (300–400 tpm) gedurende ~10 seconden.
2. Voeg component B (verharder) toe aan component A
3. Gebruik vanaf nu een elektrisch mengtoestel met dubbele mengstaaf (300-400 tpm, >700 W)
4. Voeg, tijdens het mengen van componenten A+B, geleidelijk de benodigde vulstof of aggregaten toe.
5. Geleidelijk de vereiste hoeveelheid Sika® Extender T toevoegen (zie § Verbruik).
6. BELANGRIJK - Vermijd overmatig mengen om luchtinsluiting te minimaliseren. Meng nog 2 minuten tot een homogeen mengsel is bereikt.
7. Om een grondige menging te garanderen, de materialen overgieten in een andere mengkuip en opnieuw mengen om een glad en uniform mengsel te bekomen.
8. Schraap tijdens de laatste mengfase de zijkanten en de bodem van de mengkuip ten minste eenmaal af met een vlakke of rechte spaan om zo zich te verzekeren van een volledige menging.
MENGPROCEDURE VOOR 2 COMPONENTEN PRODUCT + AGGREGATEN
1. Meng component A (hars) met een elektrisch mengtoestel met een dubbele mengstaaf (300–400 tpm,>700 W) gedurende ~10 seconden.
2. Voeg component B (verharder) toe aan component A
3. Voeg, tijdens het mengen van componenten A+B, geleidelijk de benodigde vulstof of aggregaten toe.
4. BELANGRIJK - Vermijd overmatig mengen om luchtinsluiting te minimaliseren. Meng nog 2 minuten tot een homogeen mengsel is bereikt.
5. Om een grondige menging te garanderen, de materialen overgieten in een andere mengkuip en opnieuw mengen om een glad en uniform mengsel te bekomen.
6. Schraap tijdens de laatste mengfase de zijkanten en de bodem van de mengkuip ten minste eenmaal af met een vlakke of rechte spaan om zo zich te verzekeren van een volledige menging.
MENGPROCEDURE VOOR 2 COMPONENTEN PRODUCT
1. Meng component A (hars) tot het gekleurde pigment volledig gedispergeerd is en een uniforme kleur is bereikt.
2. Voeg component B (verharder) toe aan component A.
3.BELANGRIJK - Vermijd overmatig mengen om luchtinsluiting te minimaliseren. Meng component A + B continu gedurende ~3 minuten tot een gelijkmatig gekleurd mengsel is bereikt.
4. Om een grondige menging te garanderen, de materialen overgieten in een andere mengkuip en opnieuw mengen om een glad en uniform mengsel te bekomen.
5. Schraap tijdens de laatste mengfase de zijkanten en de bodem van de mengkuip ten minste eenmaal af met een vlakke of rechte spaan om zo zich te verzekeren van een volledige menging.
VERWERKING
BELANGRIJK:
Tijdelijke verwarming
Indien tijdelijke verwarming nodig is, gebruik dan geen gas-, olie-, paraffine- of andere fossiele brandstofverwarmers. Deze produceren grote hoeveelheden kooldioxide en waterdamp, die de afwerking nadelig kunnen beïnvloeden.
- Gebruik voor verwarming uitsluitend elektrisch aangedreven warmeluchtblaassystemen.
BELANGRIJK:
Uitvoeren van proefvlakken
Alvorens een elektrisch geleidende vloer aan te brengen, moet eerst een referentievlak aangelegd worden en alle procedures overeengekomen worden met alle partijen.
BELANGRIJK:
Tijdelijk vochtscherm
Indien het vochtgehalte gemeten met de carbideflesmethode (CM) > 4% (gewichtsdelen) bedraagt, dan kan Sikafloor® EpoCem® als tijdelijk vochtscherm worden toegepast.
- Neem contact op met de technische dienst van Sika voor meer informatie.
BELANGRIJK:
Indeukingen
Onder bepaalde omstandigheden zoals bij vloerverwarming of hoge omgevingstemperaturen in combinatie met een hoge puntbelastingen, kan dit tot indeukingen in het hars leiden.
GLADDE SLIJTLAAG
Geschikt verwerkingsmaterieel
Brede vloerrakel nr. 656, getand blad nr. 25 (www.polyplan.com)
Werkwijze
- Giet het gemengde product op de ondergrond. Opmerking: Het verbruik is gespecificeerd in het hfst Verwerkingsinformatie hierboven.
- Verdeel het product gelijkmatig over het oppervlak met een getande plakspaan.
- Om een gladde afwerking te verkrijgen, het oppervlak gladstrijken met de vlakke kant van een truweel.
- Rol het oppervlak kruiselings na met een stalen prikroller.
GETEXTUREERDE SLIJTLAAG
Geschikt verwerkingsmaterieel
- Truweel nr. 999 (www.polyplan.com)
- Lijmkam nr. 777, getand blad Nr. 23 = A3 (www.polyplan.com)
Werkwijze
- Giet het gemengde product op de ondergrond. Opmerking: Het verbruik is gespecificeerd in het hfst Verwerkingsinformatie hierboven.
- Verdeel het product gelijkmatig over het oppervlak met een getande plakspaan.
- Rol het oppervlak kruiselings na met een stalen prikroller.
ZELFVLOEIENDE SLIJTLAAG MET INSTROOIING
- Giet het gemengde product op het oppervlak. Opmerking: Het verbruik is gespecificeerd in het hfst Verwerkingsinformatie hierboven.
- Verdeel het product gelijkmatig over het oppervlak met een getande plakspaan.
- Rol het oppervlak kruiselings na met een stalen prikroller. Opmerking: Hou tijdens het aanbrengen de aansluiting "nat in nat" om een naadloze afwerking te verkrijgen.
- Bestrooi het oppervlak met vuurgedroogd kwartszand of siliciumcarbide, eerst licht, daarna tot verzadiging. Opmerking: Het type aggregaat is afhankelijk van de systeemopbouw. Raadpleeg de relevante systeemfiche.
TOPLAAG VOOR INGESTROOIDE OPPERVLAKKEN
- Giet het gemengde product op het oppervlak. Opmerking: Het verbruik is gespecificeerd in het hfst Verwerkingsinformatie hierboven.
- Verdeel het product gelijkmatig over het oppervlak met een vloerwisser.
- Rol het oppervlak kruiselings na met een medium vachtroller. Opmerking: Hou tijdens het aanbrengen de aansluiting "nat in nat" om een naadloze afwerking te verkrijgen.
REINIGING GEREEDSCHAP
Reinig alle gereedschap en materieel onmiddellijk na gebruik met Sika Verdunner C. Uitgehard product kan alleen mechanisch worden verwijderd.